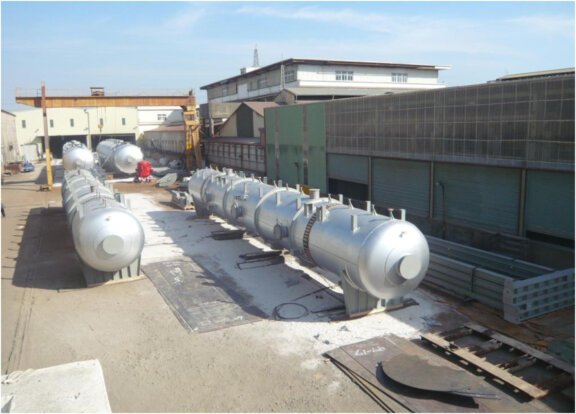
Counterflow Deaerator
Newterra Counterflow Deaerators are built for reliability in large-capacity industrial applications.
Learn More about Counterflow DeaeratorParallel Downflow Deaerators offer high performance between the extremes of 100% make-up water (below 50° F), mostly hot condensate and substantial flashing returns.
The Parallel Downflow Deaerators from Newterra are engineered for superior performance in removing dissolved gases, chiefly oxygen and carbon dioxide, from boiler feedwater, thereby averting corrosion and extending the lifespan of steam-generating systems. These deaerators utilize a parallel downflow design, which enhances contact time between water and steam, ensuring optimal gas removal efficiency. Ideal for high-capacity applications, they offer a seamless integration into large-scale industrial and utility operations. The design prioritizes energy efficiency and operational stability, reducing maintenance requirements and operating costs. Newterra’s Parallel Downflow Deaerators represent a state-of-the-art solution for organizations aiming to improve their thermal efficiency and protect their capital investments in boiler systems.
We understand your unique challenges. Beyond a technology solution, Newterra is dedicated to the entire lifecycle of your needs. Whatever support you need, Newterra probably has a solution to solve it..
Whether your needs are short-term bridge, emergency or supplemental or long-term system deployment, Newterra has flexible solutions that alleviate the need for major capital expenditure.
From operations consultation and long-term service contracts embowered by our Internet of Things (IoT) platform to commissioning expertise and emergency ad-hoc needs almost anywhere in the world, our technical experts are available to serve you. Let Newterra keep your systems optimized.
From licensed and certified removal, to exchange, to supply, Newterra provides the gamut of services to keep your media and membrane solutions at peak performance. Let the same experts who build your systems help you keep them running.
Rely on Newterra for all your aftermarket needs. Our teams have the background and tools to serve you effectively. Nothing beats original equipment manufacturer (OEM) service. Anything you need, we’re here for you.
Water enters the preheating compartment and is heated to saturation temperature. Here, the bulk of the noncondensible gases is removed before the water enters the trays.
Heated water passes through the water seal-type distributors to the tray section. The water seals prevent bypassing of steam into the preheating compartment and prevent non-condensible gases from entering the tray compartment from the preheating section. Water passes downward through the trays to complete final deaeration and then goes to storage. Steam enters the inlet nozzle and passes through ports in the tray compartment to the space above the trays, flowing downward with the water through the tray section.
This action provides highly efficient distribution over the trays, maximizing surface contact between steam and water, and prevents damming up of water and possible water hammer. Practically no steam condensation occurs in the tray compartment since inlet water has been heated to within a few degrees of steam temperature in the preheater compartment.
The entire volume of uncontaminated steam is employed in the scrubbing action, thus removing the final traces of oxygen. Steam leaves the bottom of the trays, then flows to the preheater compartment, where it is condensed. Noncondensible gases are discharged into the atmosphere.
Newterra Counterflow Deaerators are built for reliability in large-capacity industrial applications.
Learn More about Counterflow DeaeratorNewterra Multiport Relief Valves are designed for safety and to dampen the pressure swings within deaerators, steam lines and associated components.
Learn More about Multiport Relief ValvesNewterra Spray Atomizing Deaerators are built for industrial applications to supply high-purity water to maximize the efficiency and lifespan of boiler systems.
Learn More about Spray Atomizing DeaeratorNewterra UNI-PAC Packaged Deaerators capacity ranges from 10,000 lbs per hour and larger for parallel downflow, counterflow or spray-atomizing to best suit every application.
Learn More about UNI-PAC Packaged DeaeratorNewterra Deaerator and Forced Draft Degasifiers remove dissolved oxygen and carbon dioxide without steam feed or a need for raising water temperature.
Learn More about Vacuum Deaerator & Forced Draft Degassifiers