Sucrafor
A Sugar Factory Wastewater Treatment Plant Experiences a Large Reduction in BOD/COD Levels
The Newterra® Aire-O2® Triton Process Aerator/Mixers provide a reliable, efficient solution in a challenging environment.
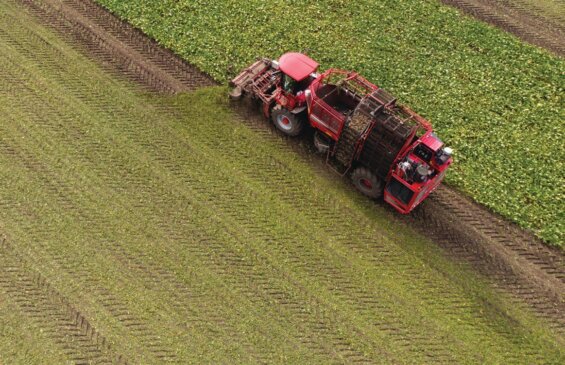
The Sucrafor sugar-factory wastewater treatment plant was challenged to meet stringent Biochemical Oxygen Demand (BOD) and Chemical Oxygen Demand (COD) standards. In this corrosive environment, sludge from previously installed equipment was an issue. Twenty (20) Aire-O2 Triton Process Aerator/Mixers were installed to combat the environment’s high organic loads and product reliability issues. BOD loads have been reduced by 99%, COD levels are well below standards, and sludge does not build up.
Sucrafor is a sugar beet processing plant in Nador, Morocco. It is part of the five companies that comprise the Cosumar Group, a manufacturer specializing in the extraction, refining, packaging, distribution and export of sugar.
Market Served
Agriculture
Application
Wastewater Treatment
Location
Nador, Morocco
Challenge
Reduction of BOD/COD Levels
Solution/Service
20 Aire-O2 Triton Process Aerator/Mixers
CHALLENGE
Sucrafor designed a wastewater treatment plant to maintain high organic loads through anaerobic, anoxic and aerated lagoons, which crush more than 5,000 tons of sugar beets daily. The plant operates for 90 days during beet processing, and the aeration equipment must be fully functional and efficient after downtime during the growing season. Sucrafor was challenged to meet stringent BOD/COD standards and provide a mechanically sound, reliable solution. Due to the high organic loads and tightening BOD/COD standards, the Newterra Aire-O2 Triton Process Aerator/Mixers were installed.
SOLUTION
Since sludge was an area of concern from the previously installed equipment, engineers at Newterra helped solve sludge issues by effectively keeping solids suspended in the aeration basins. Newterra provided 20 20hp/15kW Aire-O2 Triton Process Aerator/Mixers to achieve this. The equipment was specially designed with anti-erosion baffles to start at a water level of 4.43′ (1.35m) as the processing comes online and fills to a max level of 9.84′ (3m) water depth. The stainless components were built to withstand the corrosive environment allowing for no reduction in aeration efficiency.
RESULTS
The wastewater plant is operating efficiently with the Aire-O2 Triton Process Aerator/Mixers and sludge does not build up in the aeration basin; saving the plant time and money. After three years, the installation has positioned the mill to produce more sugar, and the plant can take on an extra load. The BOD loads have been reduced by 99%, and COD levels are now well below the required standards.
“We’re very satisfied with the Triton’s performance… the plant is now able to handle the increased load without further investment into the wastewater plant”
Impact
Salah Nahid, Director of Sucrafor, was very satisfied with the Aire-O2 Triton Process Aerator/Mixer’s strong performance. The plant now easily handles the increased load without further investment into the wastewater plant, providing significant cost savings. Maintenance has also been simplified, especially at the end of the crucial harvest season. Nahid and his team are con dent in the equipment today and know that the system will be ready to work during spring start-up as Sucrafor prepares for many successful future harvests.
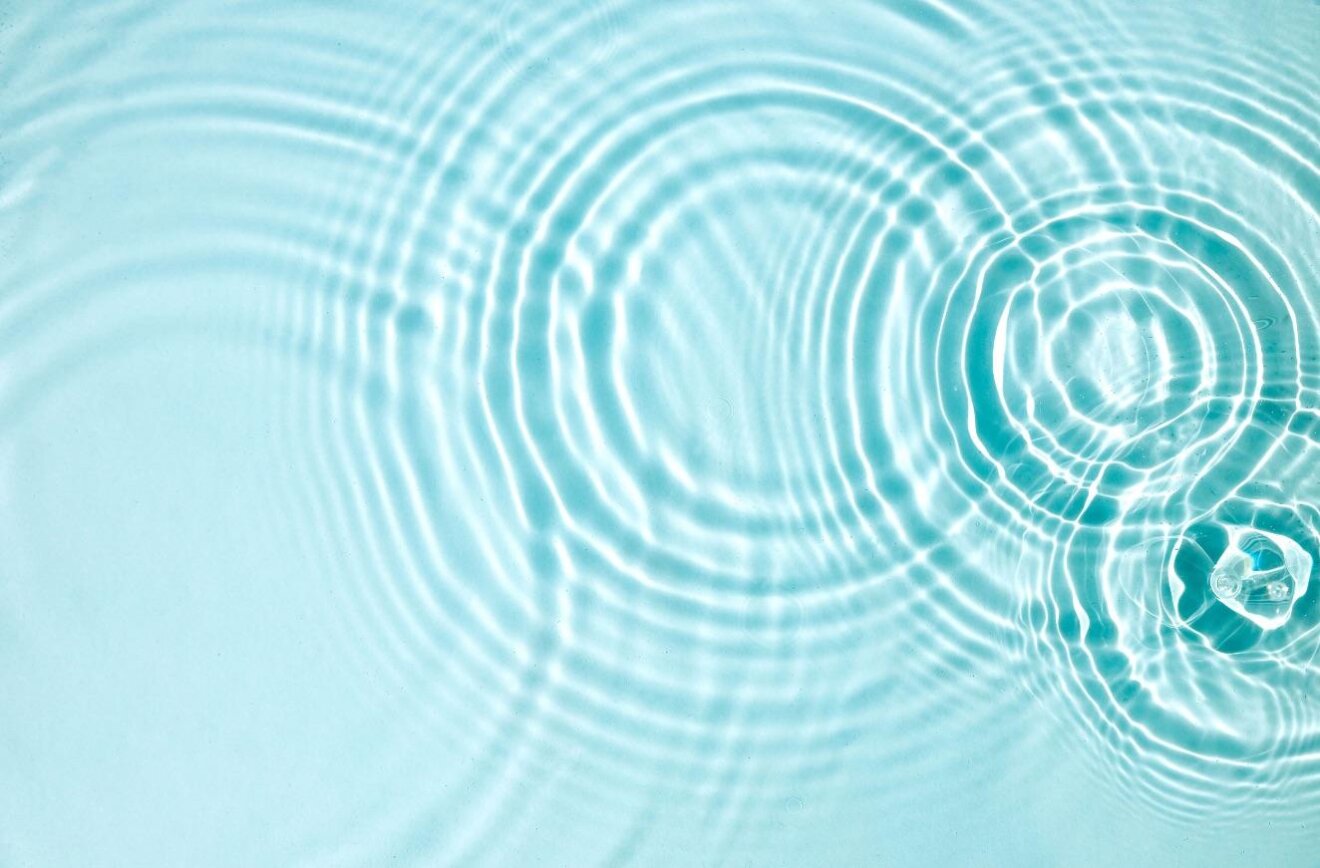
We Are Here to Help
Partner with Newterra to maximize your water resources. Together, we’ll design solutions specific to your needs in the food and beverage industry, boosting your efficiency and driving success.