Mid-West US Ethanol Refinery
Newterra Dramatically Reduces Fuel and Water Consumption While Increasing Boiler Life
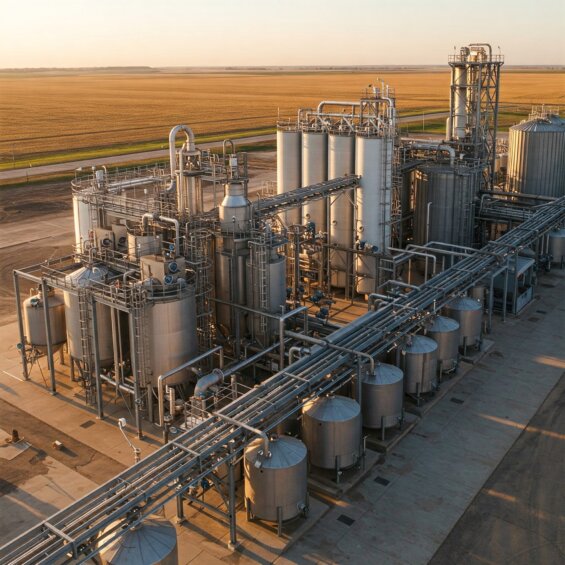
Newterra’s water treatment system cut fuel use, conserved water, and extended boiler life, driving significant cost savings.
Industry
Green Energy
Location
Midwestern US
Capacity
1,429 GPM
CHALLENGE
A major ethanol refinery in the Midwestern United States faced a significant challenge during its expansion from 40 million to 150 million gallons per year. The new plant required high-pressure boilers that demanded high-quality make-up water to operate efficiently. To achieve this, the plant needed to produce 1,000 GPM of purified water with total dissolved solids (TDS) below 5 parts per million (PPM).
SOLUTION
Newterra designed and implemented a comprehensive water treatment system to meet these needs. The solution included:
- Twin 96×840 Reverse Osmosis Systems
- One CE Triplex Permeate Polishing Softener System
- One CIP (Cleaning Station)
Water Treatment Process:
The treatment train begins with pre-filtered well water fed at a rate of 1,429 GPM. An anti-scalant is added to minimize membrane scaling, ensuring consistent performance. The water then enters the reverse osmosis (RO) systems, where 99% of TDS is removed, producing 1,000 GPM of water with TDS below 5 PPM. Afterward, the treated water undergoes pH adjustment before passing through a triplex polishing softener system to eliminate any remaining hardness minerals.
RESULTS
The high-quality make-up water provided multiple benefits for the plant:
- Reduced Boiler Blow-Down: The improved water quality minimized the need for frequent boiler blow-down, saving water and energy.
- Decreased Scale Build-Up: The clean water significantly lessened mineral deposits inside boiler tubes, improving heat transfer efficiency.
- Lower Fuel Consumption: Enhanced boiler performance reduced the amount of fuel required for operation.
- Water Savings: Reduced blow-down and scaling minimized overall water consumption.
Additionally, the Newterra-supplied cleaning station enables plant personnel to maintain RO membrane efficiency, extending the system’s lifespan and protecting the plant’s return on investment. Through this innovative solution, Newterra delivered improved system performance, increased efficiency, and substantial cost savings for the ethanol refinery expansion.

Subscribe to our Newsletter today! Receive monthly updates on the latest projects like this as well as new water treatment technologies, sustainability, and industry trends, along with exclusive insights and company news and events.
By entering your email, you agree to receive newsletters and promotional updates from Newterra. You can unsubscribe at any time.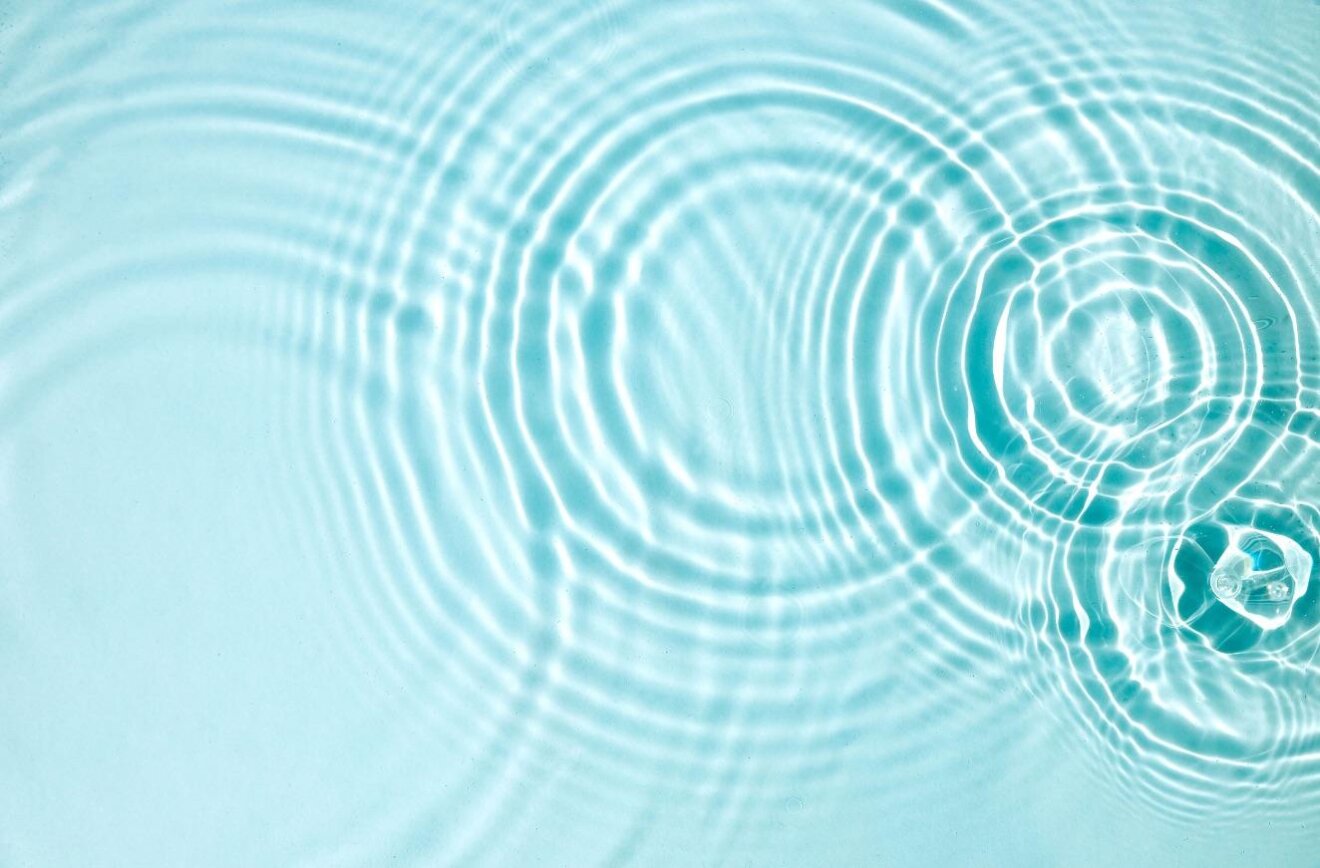
We Are Here to Help
Partner with Newterra to maximize your water resources. Together, we’ll design solutions specific to your needs in the food and beverage industry, boosting your efficiency and driving success.