A Newterra Solution Offers a “Perfect Fit” for This Client’s Expansion
Clear 3 MBR technology is deployed as a technological upgrade to accommodate major growth at a busy hatchery allowing it to achieve strict discharge requirements.
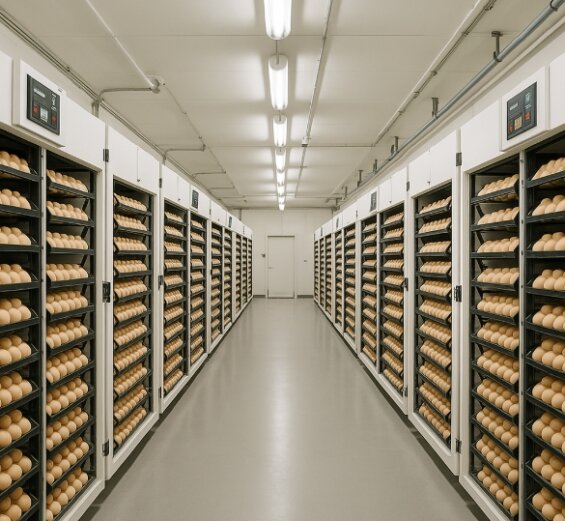
To accommodate growth, a poultry hatchery needed to expand its Canadian facility to accommodate increased hatching of turkeys and broiler chicks and remodel the original hatchery to accommodate the addition of new equipment. The operation runs continuously, 365 days per year, producing 20 million broilers and 2 million turkeys annually.
Industry
Food & Beverage
Location
British Columbia, Canada
Application
Industrial Wastewater Treatment
THE CLIENT
This Poultry Hatchery is one of Canada’s most trusted and recognized poultry brands, known for its commitment to quality, innovation, and food safety. With decades of experience in poultry processing, the hatchery operates multiple facilities across the country and plays a key role in supplying premium chicken and turkey products to Canadian households.
CHALLENGE
Proper wastewater treatment (wash water) in a poultry hatchery is beneficial in many ways, such as protecting the environment, safeguarding human health, regulatory compliance, conserving resources, controlling odors, and promoting overall sustainability in poultry production. The current treatment of the hatchery’s wash water had been addressed by an aging Rotating Biological Contactor (RBC) System that desperately needed replacement. The hatchery needed a better alternative to meet the strict discharge requirements that would allow effluent of sufficient quality to continue direct discharge into the local watershed under new, more stringent environmental requirements. Wash down water from the hatchery is high in BOD (Biochemical Oxygen Demand) and solids, as well as ammonia, thus requiring the inclusion of an Anoxic Tank in the treatment process.
SOLUTION
The Newterra Clear3 Membrane Bioreactor (MBR) System was ultimately selected for the hatchery based the ability to maintain all required discharge levels even when run for short periods at more than double the design flow. In addition, Newterra was able to offer technical expertise, manufacturing capability, and lifecycle equipment support for the long-Term. The Clear3 MBR System offers a compact footprint and is housed in an ISO-certified container for easy set-up. The membrane tanks feature side door access to the modules which simplifies periodic maintenance and eliminates the need for roof access. The Clear3 MBR System even maintains all required discharge levels – even when running at more than double the 22 m3 /day (5,811 gpd) design flow of the system
Newterra empowers industry to meet regulatory compliance and surpass environmental discharge regulations, shielding your company from legal issues and fines. Simultaneously, it fosters resource conservation through water recovery and reuse, contributing to sustainability and cost savings by reducing freshwater demand.
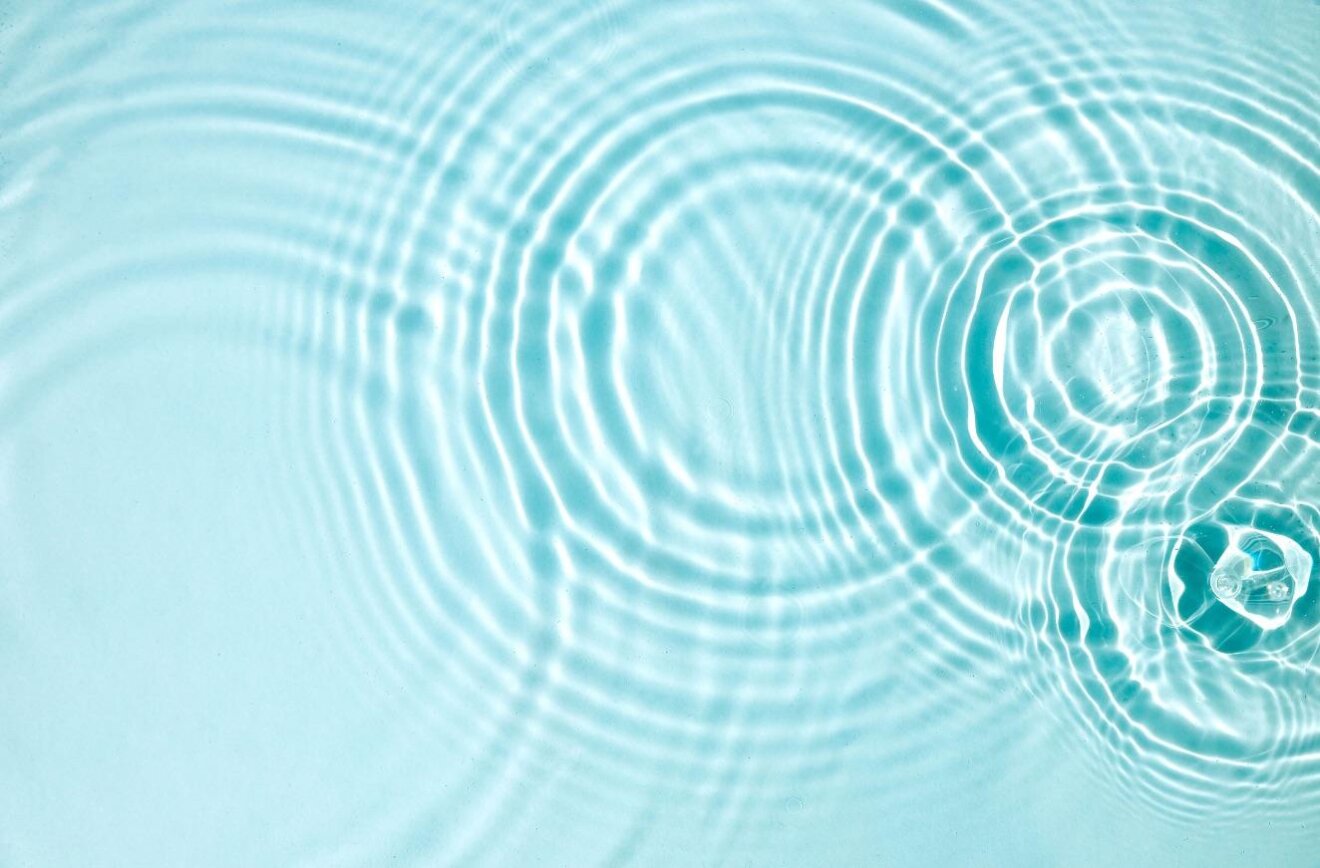
We Are Here to Help
Partner with Newterra to maximize your water resources. Together, we’ll design solutions specific to your needs in the food and beverage industry, boosting your efficiency and driving success.