Bristol Meyers Squib
Optimizing Water Purification at a Pharmaceutical Plant with Newterra’s RO-Based Solution
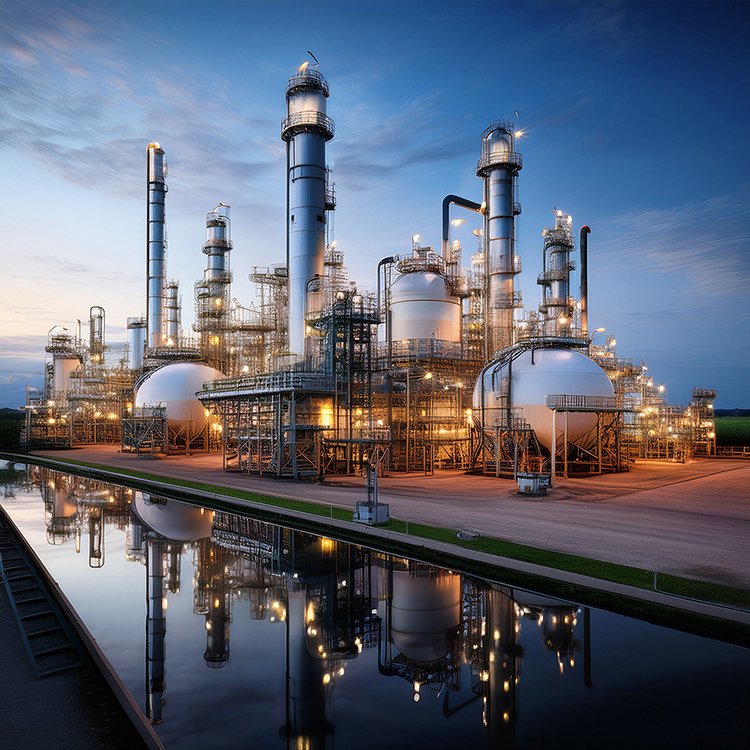
Newterra’s RO-based solution transformed a Syracuse pharmaceutical plant by cutting hazardous material handling, saving $63,000 annually, and enhancing operational efficiency with a modular, space-saving system.
Industry
Pharmaceutical
Location
Syracuse, NY
Capacity
120 GPM
CHALLENGE
A major pharmaceutical plant in Syracuse, NY faced challenges with handling acids for regenerating their high-purity water system used for boiler make-up. The operators sought a solution to reduce costs, minimize hazardous material usage, and fit within a limited space. They were interested in whether a Reverse Osmosis (RO) system could address these issues.
In the pharmaceutical industry, wastewater treatment is crucial for environmental protection, regulatory compliance, and public health. Proper treatment removes harmful substances like active pharmaceutical ingredients and chemicals, preventing pollution and protecting ecosystems. Adhering to regulations also avoids fines and preserves the company’s reputation, ensuring sustainable and responsible operations.
SOLUTION
Newterra implemented a tailored water purification system consisting of:
Twin-Bed Multimedia Filter: For effective pre-treatment.
Sodium Zeolite Polishers: To ensure high-purity water.
Clean-In-Place (CIP) System: To simplify maintenance.
The RO system was designed to address the space constraints by using two 60 GPM units, which could be combined to achieve a total capacity of 120 GPM. This modular approach allowed the units to fit through plant doorways and be integrated seamlessly.
RESULTS
The Newterra solution significantly reduced the handling of hazardous materials and provided a net savings of $63,000 annually. The twin RO units offered operational
flexibility, allowing them to run together at full capacity or independently, thus ensuring system redundancy and reducing the risk of unplanned outages. The CIP system streamlined operation and maintenance, ensuring a reliable supply of high-purity water.
Additionally, the plant benefited from a reduced carbon footprint due to increased boiler efficiency and water savings, further enhancing operational sustainability.
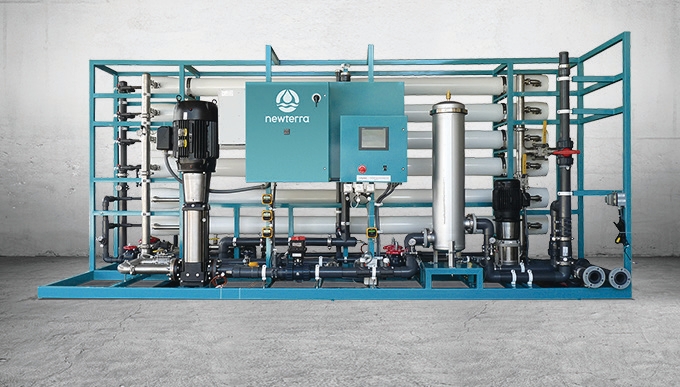
for a total capacity of 120 GPM, addressing space constraints
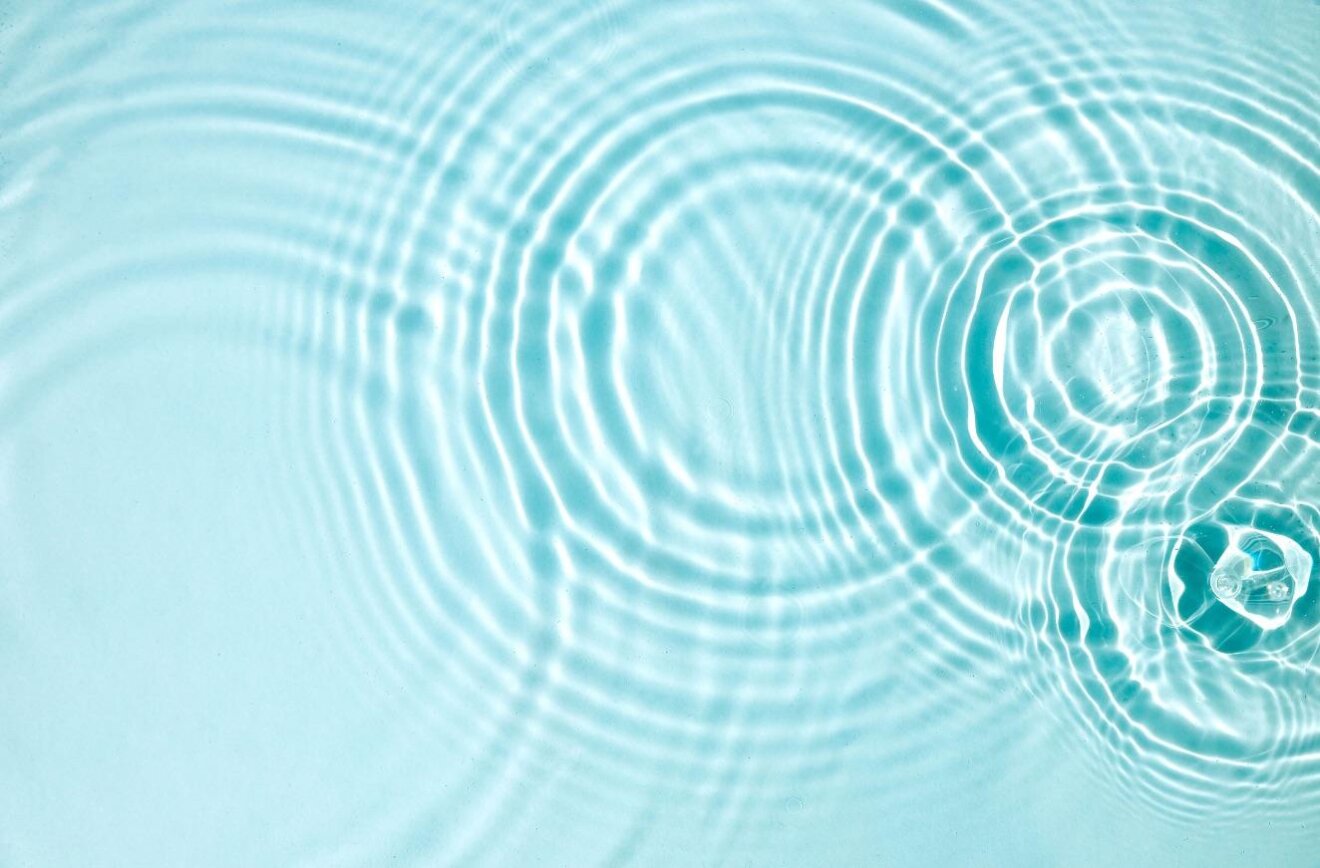
We Are Here to Help
Partner with Newterra to maximize your water resources. Together, we’ll design solutions specific to your needs in the food and beverage industry, boosting your efficiency and driving success.